电磁法检测是一种较成熟的非接触式埋地金属管道缺陷检测方法,其一般采用过零点时间、信号峰值、峰值时间及信号晚期的衰减率等参数来评价管道壁厚。在检测中,要获取一个完整的检测信号必须设置合理的激励参数,如果参数选择不当,可能会导致管道壁厚检测数据偏移,造成误检或者漏检。
为了便于根据不同管道规格或实际工况选择合理激励参数,陕西国防工业职业技术学院智能制造学院和中煤科工集团西安研究院有限公司的研究人员对电磁法检测金属管道缺陷的影响因素展开研究。
电磁法检测原理
电磁法检测金属管道的原理如图1所示,通过信号发生器给传感器施加阶跃型电流信号,在空间产生稳定的一次磁场,一次磁场扩散至金属管道表面形成涡流效应,由于电流信号存在阶跃过程,在电流从高电位瞬间转变为低电位时,根据法拉第电磁感应定律可知,金属管道表面的涡流会在空间产生与一次磁场相同的二次磁场,二次磁场携带管道的基本信息被传感器接收传并输至电脑端,进一步分析该信号即可评价管道。
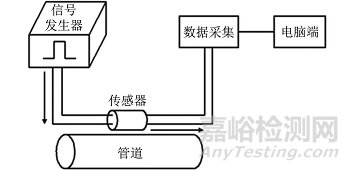
图1 电磁法检测金属管道原理示意
根据电磁法原理和检测方法可知,激发电流的大小、频率、传感器提离高度等因素对接收信号的影响较为明显。为此,通过合理设计试验装置及方法,研究各影响参数对瞬变电磁检测信号的影响,以期为后续该技术在实际工况中的应用提供数据基础,提高工作效率及检测结果的准确性,满足实际工况的精度要求。
电磁法检测管道缺陷可行性分析
1、试验平台
电磁检测装置主要包括信号激发模块、传感器模块和数据处理模块,如图2所示,其中信号激发模块采用GBH-1型数据采集设备,该设备不仅采集频率可调且信噪比高;传感器采用自制线圈,结构为圆环形,其激发线圈直径为200 mm,接收线圈直径为100 mm。
图2 电磁检测装置外观
为了进一步简化试件,把管道直径放大至无限大,则管道曲面可类比于平面,因而采用钢板代替金属管道。根据传感器尺寸计算出传感器有效覆盖面积为400 mm,选取钢板尺寸的长度和宽度均为400 mm,厚度分别为5,10,15,20 mm,如图3所示。
图3 钢板试件外观
2、试验结果分析
针对不同厚度的试件展开试验,分析不同壁厚对信号的影响。设置激励电流为1 A,激发频率为1/4 Hz,试件距离传感器垂直高度为100 mm。对试验数据进行坐标变换,将笛卡尔坐标系变换成双对数坐标系后,可明显看出检测信号在t<16.326 ms时数据重合,在t>16.326 ms时出现了明显的分叉,如图4所示。检测结果表明电磁法检测金属管道缺陷具有可行性。
图4 不同厚度钢板的电磁检测信号
影响因素试验分析
1、激发频率对检测信号的影响
试验采用的激励信号为阶跃型电流信号,设备集激发和采集于一体。选择激励频率为1/16,1/8,1/4,1/2,1,2,4,8,16 Hz,分析各厚度试件在不同频率下的电磁检测信号,试验结果如图5所示。
图5 各试件不同频率下的电磁检测信号
通常,一个完整的检测信号(坐标变换后)包含两部分:直线形式的前半部分,指数形式的后半部分。由图5可以明显看出频率变化不会对幅值和幅值衰减速度造成影响,只会影响检测信号的完整性,随着频率增大,检测信号持续时间缩短,只呈现出直线部分。通常需要检测信号的后半部分来计算金属管道剩余壁厚,因此应选择合适的频率进行检测,为后期数据处理提供基础。
为了确保接收信号的完整性,必须根据管道壁厚设置合适的激发频率。分析可知对于壁厚较大的管道应该选择较小的激发频率(更有穿透力);对于壁厚较小的管道应该选择较大的激发频率,确保信号的有效性。在试验过程中发现频率小会延长数据采集时间且给后期数据带来较大干扰。为了提高实际检测工作效率,按照不同管道壁厚对激发频率进行优化,优化结果如下:
2、激励电流对检测信号的影响
根据上述频率试验的结果,为确保检测信号的完整性,选择激发频率为1/4 Hz,电流分别为0.7,1,1.5,2,2.5 A,对各试件进行检测,各试件不同电流下的电磁检测信号如图6所示。
图6 各试件不同电流下的电磁检测信号
由图6可知,对于厚为5,10,15 mm的管道,随着电流的增加,感应电动势在前期幅值增大,后期发生重合且壁厚越大重合时间越推迟;对于厚为20 mm的管道,随着电流的增加,感应电动势幅值增大且变化趋势一致。由此可知,对于壁厚较大的管道可以通过改变激励电流来获取幅值不一样的信号,对于薄壁管道,改变激励电流的意义不大,且激励电流较小时感应电动势不会发生变化,例如当管道壁厚为10 mm时,激励电流为0.7 A和1 A时感应电动势几乎一致。
时间为10.488 ms时,激励电流对感应电动势的影响规律如图7所示,可见相同激励电流下,管道壁厚越薄,获取的感应电动势越大,且随着电流的增加,感应电动势呈直线衰减。因此在实际工况作业时,较厚的管道应该选择较小的激励电流,以确保准确评价管道质量。
图7 激励电流对感应电动势的影响规律(时间为10.488 ms)
3、传感器提离高度对检测信号的影响
传感器提离高度是指传感器几何中心与正下方待检金属管道表面最高点的垂直距离。为确定提离高度与检测信号是否存在某种关系,采用控制量法设计试验组,设置激励电流为1 A,频率为1/4 Hz,提离高度分别为0,50,100,150,200,250 mm,对各试件进行试验,试验布置如图8所示。
图8 提离高度影响试验布置示意
各试件不同提离高度下的电磁检测信号如图9所示,可以明显看出,提离高度增大感应电动势幅值也随之增大;当提离高度增大到100 mm时,各试件的感应电动势出现波动,原因在于试验使用的传感器直径为200 mm,试件边长为400 mm,其有效覆盖范围L=D+2h(L为试件边长,D为传感器直径,h为提离高度),故其有效提离高度为100 mm。通过Origin软件分析曲线衰减率可知,提离高度增大只会影响感应电动势幅值,不会对感应电动势衰减率造成影响,由此可以降低实际检测时的操作难度,消除传感器高度不一对管道缺陷评价造成的误差。
图9 各试件不同提离高度下的电磁检测信号
4、缺陷位置对检测信号的影响
瞬变电磁法对轴向缺陷定位准确度较高,但对于周向分布缺陷的试验数据较少。选择规格为ф108 mm×6 mm的管道作为试件,在传感器有效覆盖范围内制作人工缺陷,模拟管道在实际环境遭到的腐蚀,缺陷类型为均匀腐蚀,规格为120 mm×120 mm×2 mm。设置激励电流为1 A,频率为1 Hz,提离高度为50 mm,将缺陷放置于传感器正下方的位置,如图10所示。
图10 缺陷位置影响试验布置示意
缺陷位置对感应电动势的影响规律如图11所示,可见当缺陷在管道正下方(0°)时,感应电动势最小,当缺陷周向旋转时,感应电动势随之增大,当管道旋转180°时,感应电动势出现最大值,随之又慢慢减小,但都小于管道无缺陷处的感应电动势。试验结果表明,瞬变电磁法对传感器正下方的缺陷检测灵敏度较高,可为该技术应用拓展至城市热力、压力管道缺陷评价提供参考价值。
图11 缺陷位置对感应电动势的影响规律
5、缺陷类型对检测信号的影响
调研资料表明,油气管道偶尔也会出现穿孔腐蚀。为判断缺陷类型对检测信号的影响,使用上述管道作为试件,设置激励电流为1 A,频率为1 Hz,提离高度为50 mm。在管道上制造3个均匀腐蚀、2个穿孔腐蚀,这5个缺陷体积均为传感器覆盖区域总体积的5%,缺陷规格及分布如图12所示,电磁检测结果如图13所示。
图12 管道人工缺陷规格及分布示意
(缺陷1深0.5 mm,整周;缺陷2深1 mm,半周;缺陷3深1.5 mm,1/4周)
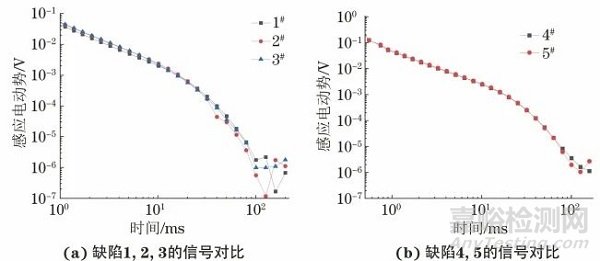
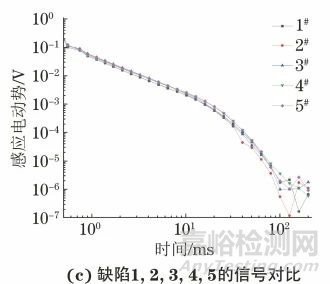
图13 缺陷类型对电磁检测信号的影响规律
分析图13可知,在传感器有效覆盖范围内,若缺陷类型相同,体积相同,则感应电动势幅值和衰减趋势几乎一样;当均匀腐蚀和穿孔腐蚀同时存在,可以看出穿孔腐蚀的感应电动势幅值比均匀腐蚀的感应电动势幅值高且衰减较慢。由此可见,在实际检测中,穿孔腐蚀不易被发现,很容易被误判。因此建议通过优化传感器结构或使磁场聚焦来检测孔状腐蚀。
结论
(1) 不同壁厚钢板的检测信号在t<16.326 ms时重合,在t>16.326 ms时出现明显的分叉,表明电磁法在金属管道缺陷检测中具有可行性。
(2) 对频率、电流、提离高度和缺陷类型等影响参数的试验表明,频率只会对检测信号的完整性造成影响;激励电流变化对检测信号幅值和衰减速度影响不大;提离高度影响检测信号的幅值,对衰减率无影响;在传感器有效覆盖范围内,缺陷处于传感器正下方时最容易被发现;当缺陷体积相同时,均匀腐蚀要比穿孔腐蚀更容易发现。
(3) 试验结果不仅在传感器优化及实际工况作业中具有重要的指导意义,还对具有包覆层金属管道的腐蚀和缺陷检测有借鉴意义。

来源:无损检测NDT
关键词:
电磁法
油气管道缺陷